Reconfigurable wheel track system
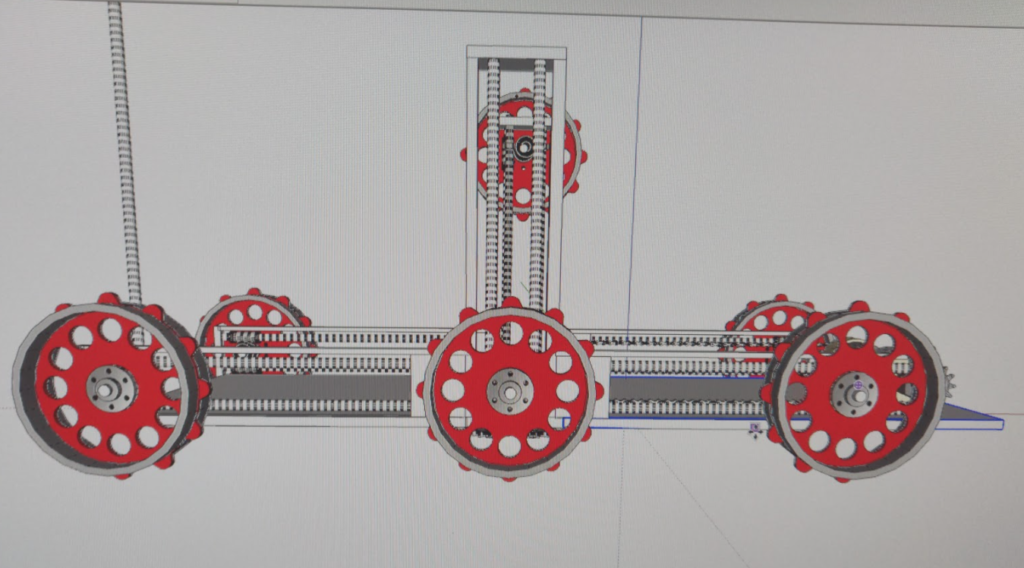
Working principle
It works on the principle of variable traction and surface friction with a change in contact surface area of wheel/track with a road or off-terrain surface. Such a robot works like a military tank when the track is in a normal position and on flat surfaces like roads it changes its track into a triangular shape so as to improve its capability of adaptation not only to complex terrain with obstacles but also by adapting to flat surfaces by using a track transformation mechanism, the robot has two kinds of locomotion configurations: triangular configuration and normal track configuration. The robot works in the triangular track mode when it moves on an even and smooth ground to obtain better efficiency for better locomotion. In the case that it encounters obstacles such as vertical stairs sand, gravel, grass and other complicated terrains, the robot will transform itself into the climbing mode with the assistance of the lead screw and scissor linkage mechanism, in this case, the tracked wheel will rotate the belt tracks to overcome the higher obstacle
Reconfigurability of the robot’s locomotion modes is implemented by a re-adjustable system, which comprises an actuating system, and a pair of symmetric reconfigurable frames that are incorporated with two geared motors connected with tracked wheels and each of which is connected by scissor linkage. As shown in Fig. above and in the video below, the actuating system contains the stepper motor, the nut, the lead screw and sliding block and rod, and the geared motor incorporated with the driving frame through the sliding mechanism, which provides driving torque for the reconfigurable frame. The reconfigurable frame is mainly made up of a Watt II linkage which contains the V-shaped link, T-shaped link, link A, link B, link E and link 60 F; and together with the geared track wheels leads to reconfiguring the deformable track belt from the wheeled shape to the triangular-tracked shape or vice versa
OBJECTIVES
The main objective of this project is to design and evaluate devices that combine the benefits of both wheels and tracks. The second objective of this project is to evaluate designs for a wheel of reconfigurable width and diameter and use a trial and error to select the best candidate design. Then we will fabricate a re-adjustable wheel system of the chosen design and compare its efficiency and change in power output values in each of the terrain and soil varieties to the values produced by a non-reconfigurable vehicle. We will also be designing or finding a testbed in order to conduct those tests.
As this project was made in 2018, only few images and videos were available in my storage which are attached below.
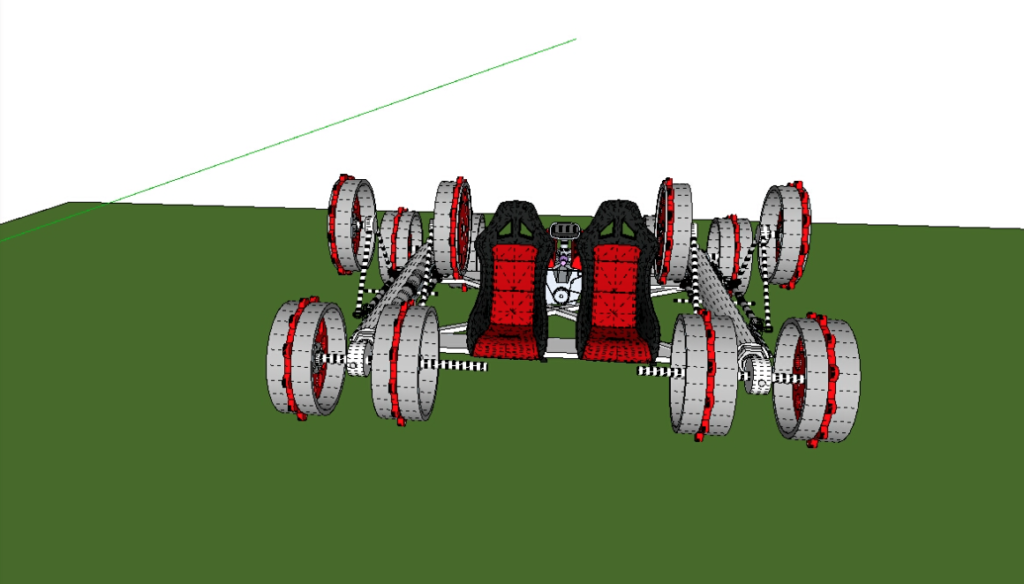